Imagine driving down a winding road, enjoying the scenery, when suddenly, you need to hit the brakes. But instead of a smooth, quiet stop, you hear a screeching noise and feel a jolt. Not the experience you were hoping for, right? The culprit could be improper brake grease application, an often overlooked aspect of vehicle maintenance. In this blog post, we’ll dig into the world of brake grease and provide you with all the knowledge you need, including where to apply grease to brake pads, to ensure optimal brake performance, reduce noise, and protect your vehicle’s components.
From the importance of brake grease and the different types available to proper application techniques and maintenance tips, we’ve got you covered. Say goodbye to screeching brakes and hello to a smoother, safer driving experience with our guide on where to apply grease on brake pads.
Contents
- 1 The Importance of Brake Grease
- 2 Proper Greasing Techniques for Disc Brake Pads
- 3 Effective Lubrication for Drum Brakes
- 4 Tips and Best Practices for Brake Grease Application
- 5 When to Apply Brake Grease
- 6 Summary
- 7 Frequently Asked Questions
- 7.1 Should you put grease on brake pads?
- 7.2 Where does copper grease go on brake pads?
- 7.3 Can you put too much grease on brake pads?
- 7.4 Where do I apply brake grease on brake pads?
- 7.5 What kind of grease should I use on brake pads?
- 7.6 How much grease should I use on brake pads?
- 7.7 Can I use brake fluid instead of grease on brake pads?
- 7.8 How often should I apply grease to brake pads?
Short Summary
- Brake lube grease is essential for optimal brake performance and offers multiple benefits, including smoother operation.
- Different types of brake grease should be selected based on the vehicle’s components, while proper application techniques involve greasing caliper pistons, backing plates, or shims with a high-temperature synthetic/ceramic or molybdenum grease.
- Regular maintenance checks are necessary to optimize braking system performance. When replacing brake pads, ensure that they are properly lubricated for noise reduction and improved pedal feel.
The Importance of Brake Grease
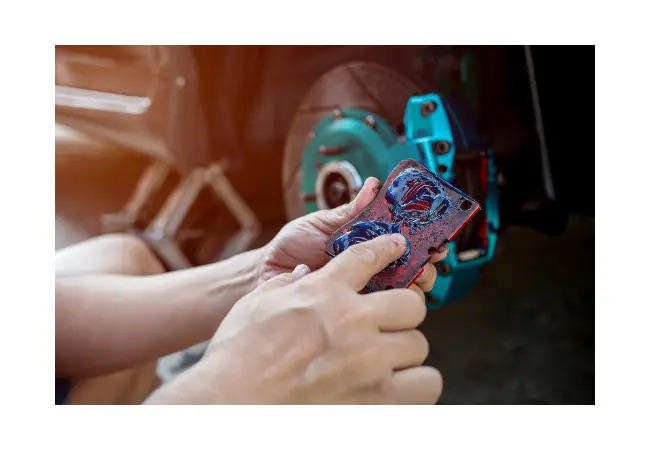
Brake grease plays a pivotal role in ensuring optimal brake performance. It helps minimize noise and friction, safeguarding rubber seals and other components in the process. Its vibration-dampening properties make it an effective brake lubricant, often referred to as brake lube.
For plastic and rubber components in the brake system, a synthetic, non-petroleum, or silicone-based lubricant is recommended. To achieve the best results, it’s essential to understand the various types of brake lube and how to apply brake grease correctly.
Benefits of Using Brake Grease
Using brake grease offers multiple benefits, such as keeping the brakes lubricated and functioning optimally, especially in areas where pads slide within the caliper housing. By applying brake lubricant on the friction surface of sliding components like the caliper housing, and caliper piston, smoother movement is facilitated, brake noise is reduced, and the brake pedal feel is improved.
Aside from ensuring smooth operation, brake grease also helps protect the brake system from wear and tear. The lubricant forms a protective barrier against moisture and debris, preventing corrosion and premature wear on brake components. This prolongs the lifespan of your disc brakes and helps prevent costly repairs down the road.
Types of Brake Grease
Various types of brake grease are available, such as mineral oil-based, synthetic oil-based, and silicone-based. Each type has its specific applications and benefits. For instance, silicone-based brake lube is typically used for lubricating caliper and wheel cylinder assembly operations.
Understanding the differences between these types of brake grease will help you choose the most suitable one for your vehicle’s needs and ensure optimal brake performance.
Proper Greasing Techniques for Disc Brake Pads
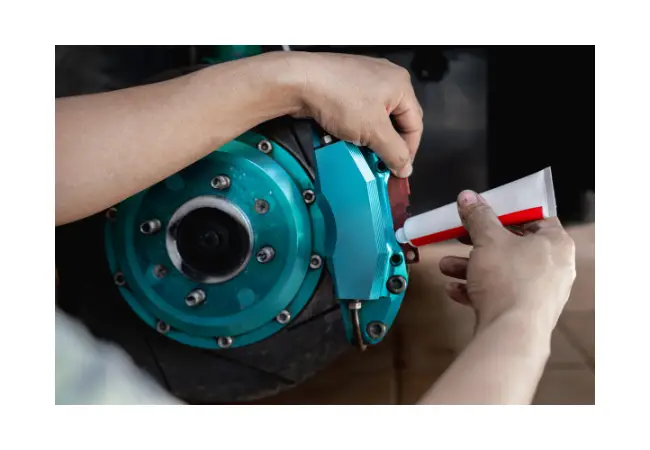
When it comes to disc brake pads, applying grease to the right components is crucial. Proper greasing techniques are involved when you apply brake grease to caliper pistons and backing plates or shims. Utilizing a high-temperature synthetic/ceramic or molybdenum grease for these components is advised.
Let’s explore how to identify the key components and apply brake lubricant correctly for optimal brake performance.
Identifying Key Components
A disc brake pad consists of three essential elements: friction material, backing plate, and adhesive. The friction material is the component that interacts with the brake rotor, generating the friction needed to slow and stop the vehicle. The backing plate serves as structural support for the brake pad, ensuring the friction material remains in its correct position. The adhesive secures the friction material to the backing plate, keeping the brake pad in place.
When you apply brake grease to the friction material, a thin, even layer is recommended. The same method should be applied to the backing plate. For the adhesive, a uniform, thin layer of brake lubricant is advised.
By correctly identifying and lubricating these key components, you can ensure the smooth operation of your disc brake pads.
Applying Brake Grease to Caliper Pistons
When you apply brake grease to caliper pistons, it’s essential to first identify the rubber components and the edges of the pad mounting tabs. Utilize high-temperature silicone (dielectric) brake grease for caliper slide pins and caliper bracket abutments. Avoid using anti-seize, as it is not suitable for these components.
To insert the pistons into the bore, gently press them in, ensuring they are properly seated. The dust boot should also be seated to protect the piston and prevent debris from entering the caliper piston bore.
Properly greasing caliper pistons and caliper slides not only ensures smooth operation but also prolongs the lifespan of the brake components after your next brake job.
Greasing Backing Plates and Shims
Backing plates and shims serve as a cushion between the brake pad and the caliper, providing noise suppression and structural support. To grease these components, apply a high-temperature synthetic/ceramic or molybdenum grease on the back of a bare pad or between the pad shim.
However, it’s crucial to avoid applying grease between the pads and noise suppression shims, as this can negatively affect brake performance.
Effective Lubrication for Drum Brakes
Drum brakes require different lubrication techniques compared to disc brakes. To ensure optimal brake performance, apply brake lube to the wheel cylinder assembly work, parking brake linkage, and cables.
In the following sections, we’ll discuss how to locate the essential parts of the drum brake system and apply brake lubricant effectively.
Locating Essential Parts
A drum brake system comprises several components, including brake shoes, brake drum, wheel cylinder, anchor plate, adjuster, return springs, and fastening/actuating elements. Each component serves a specific purpose, such as generating friction to slow the vehicle (brake shoes), driving the brake shoes against the drum (wheel cylinder), or securing the brake shoes in place (anchor plate).
These components are situated in various locations within the brake drum, with the brake shoes on either side of the drum, the wheel cylinder at the top, the anchor plate at the bottom, the adjuster at the top, the return springs at the bottom, and the fastening/actuating elements at the top and bottom of the brake drum.
By familiarizing yourself with these components and their locations, you’ll be better equipped to apply brake lube effectively.
Applying Brake Grease to Wheel Cylinder Assembly Work
The wheel cylinder assembly comprises the wheel cylinder, piston, dust boot, and return spring. To lubricate these components, use silicone-based brake grease, which is ideal for rubber and plastic parts. Visually inspect the wheel cylinder assembly for any signs of grease leakage, and use a clean cloth or paper towel to remove any excess grease.
Proper lubrication of the wheel cylinder assembly not only ensures smooth operation but also protects the components from premature wear. By applying the appropriate brake lubricant and regularly inspecting the assembly, you can maintain optimal brake performance and prolong the life of your drum brakes.
Lubricating Parking Brake Linkage and Cables
The parking brake cable and associated linkages or moving parts also require lubrication for optimal brake operation. When lubricating these components, use a suitable lubricant such as Fluorocarbon Gel 880 PTFE thickened, NLGI grade 2, and consult your car’s manual or mechanic for further instructions.
By applying the correct lubricant to the parking brake cable and linkage, you can ensure proper brake functioning and prolong the lifespan of these components.
Tips and Best Practices for Brake Grease Application
To achieve the best results when you apply brake grease, it’s important to follow certain tips and best practices. These include selecting the right type of brake lubricant, avoiding common mistakes, and maintaining rubber seals and friction surfaces.
By adhering to these guidelines, you can ensure optimal brake performance and prolong the life of your brake components.
Selecting the Right Brake Grease
Choosing the right brake grease is crucial for effective lubrication and protection of brake components. Synthetic, non-petroleum, or silicone-based brake lubricants should be used for areas with plastic or rubber components. Petroleum-based lubricants must be avoided in these cases. For metal-on-metal components, opt for a dry film lubricant containing graphite or molybdenum disulfide, as petroleum-based materials can damage plastic and seals.
It’s also essential to follow the manufacturer’s guidelines for your specific brake system when selecting brake lubricant. By using the appropriate type of grease for your vehicle’s needs, you can ensure optimal brake performance and protect the components from premature wear and damage.
Preventing Common Mistakes
A few common mistakes to avoid when you apply brake grease include using too much grease and using the wrong type of grease, such as general-purpose chassis grease. These mistakes can lead to decreased brake performance, accelerated wear on brake components, and even brake failure.
To prevent these errors, always use the right type of grease for the specific components and materials, and apply only the necessary amount of lubricant. Additionally, ensure that the grease is applied to the appropriate components of the brake, following the guidelines outlined in this blog post.
Maintaining Rubber Seals and Friction Surfaces
Preserving rubber seals and friction surfaces is vital for minimizing wear on the rubber, which can lead to premature malfunction. To lubricate seals, add lubricant to the rubber compound before molding or treat the seal post-molding with silicone oil or Molybdenum disulfide.
By maintaining rubber seals and the friction surface in optimal condition, you can prolong the life of your brake components and ensure their proper functioning.
When to Apply Brake Grease
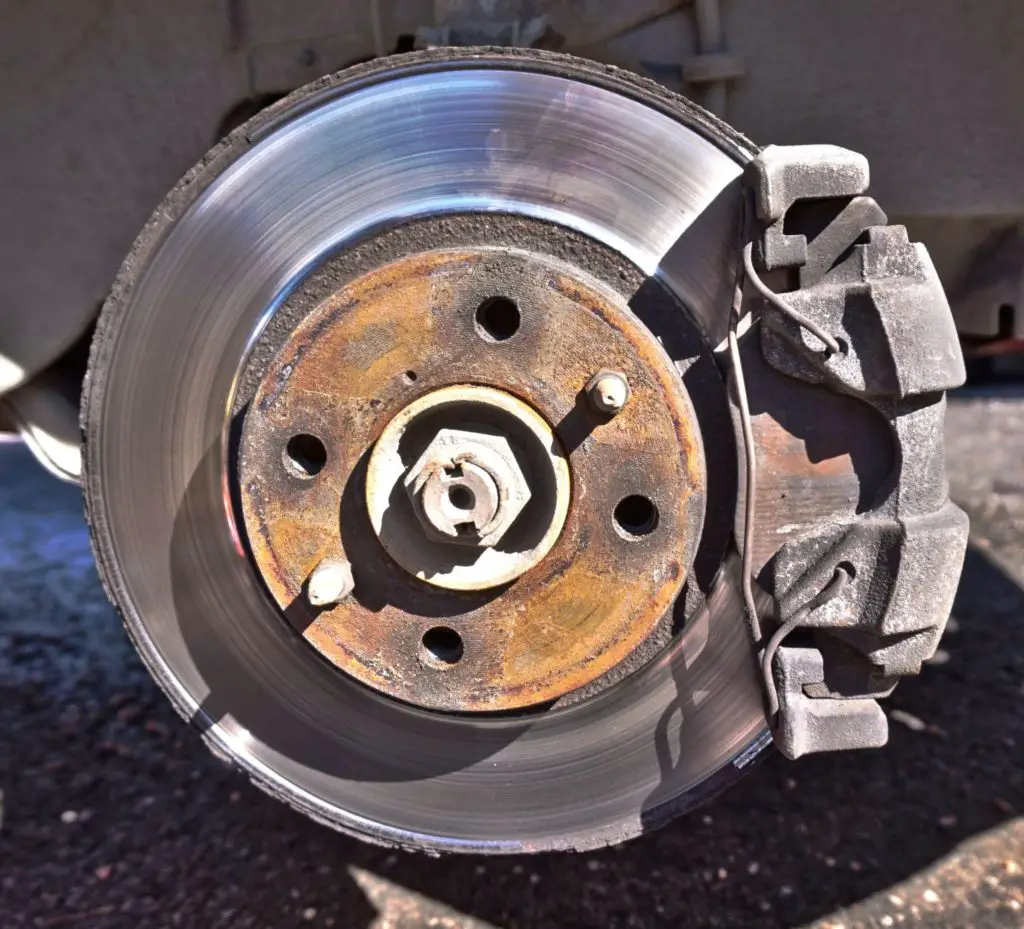
Knowing when to apply brake grease is essential for maintaining optimal brake performance. Brake grease should be applied during new brake installations, brake pad replacements, and as part of regular maintenance checks.
In the following sections, we’ll discuss each of these scenarios in more detail, providing guidance on when and how to apply brake lubricant effectively.
New Brake Installations
During new brake installations, it is crucial to apply brake grease to metal-to-metal friction points on the back of the pads and to use brake caliper grease on self-adjuster mechanisms on rear disc brakes with locking calipers, parking brake cables, and linkages. Lubricating all moving or sliding components ensures noise-free braking and proper system operation.
When you apply brake grease during new brake installations, you can ensure the smooth operation and longevity of your vehicle’s braking system.
Brake Pad Replacements
When replacing brake pads, it’s essential to apply brake grease sparingly to the back of a bare pad or between the pad shim and caliper, but not between the pads and any noise suppression shims. This ensures proper lubrication and prevents brake noise without compromising brake performance. By following these guidelines, you can effectively prolong the life of your brake pads and maintain optimal brake performance.
Regular Maintenance Checks
Regular maintenance checks are crucial for maintaining your vehicle’s braking system in optimal condition. It is recommended to inspect and lubricate the brake system approximately every 12-15 thousand miles or annually.
During these checks, apply brake grease to the necessary components, following the tips and best practices outlined in this blog post. By doing so, you can ensure smooth, noise-free braking, and prolong the life of your brake components.
Summary
In conclusion, how to apply brake grease is an essential component of your vehicle’s braking system, ensuring optimal performance, reduced noise, and protection of seals and other components. By understanding the different types of brake grease, proper application techniques, and maintenance practices, you can maintain your vehicle’s brakes in peak condition and enjoy a smoother, safer driving experience.
So next time you hit the brakes on that winding road, you’ll be greeted by a smooth, quiet stop, knowing that you’ve taken the necessary steps to care for your vehicle’s braking system. Happy driving!
Frequently Asked Questions
Should you put grease on brake pads?
As a general rule, it is not recommended to apply grease directly onto brake pads. However, proper lubrication of the other components in the braking system is necessary for optimal performance and should be done with an appropriate product. A thin layer is all that’s needed.
Where does copper grease go on brake pads?
Copper grease can help keep your brake pads from squealing, corroding and sticking. A thin coat should be applied to the back of the brake pads and also between the calipers and the pad. This will help ensure your brake system is working at optimal levels and that your brakes remain quiet.
Can you put too much grease on brake pads?
It is not recommended to use too much grease on brake pads as it can attract debris and dirt, and cause the caliper pistons to stick. Over time, the lubricant can harden to a concrete-like substance that can be damaging to the rubber of the calipers.
Where do I apply brake grease on brake pads?
When you apply brake grease – it should be applied to the back of the brake pads, where they contact the caliper. This will help to keep the brake pads moving freely and prevent them from sticking to the caliper.
What kind of grease should I use on brake pads?
You should use a high-temperature grease that is specifically designed for brake applications. This type of grease will be able to withstand the high temperatures that are generated when the brakes are applied.
How much grease should I use on brake pads?
You should only use a very thin layer of grease on the back of the brake pads. Too much grease can actually cause the brake pads to stick to the caliper.
Can I use brake fluid instead of grease on brake pads?
No, you should not use brake fluid on brake pads. Brake fluid is a hydraulic fluid that is used to transmit pressure from the brake pedal to the brake calipers. It is not a lubricant and will not help to keep the brake pads moving freely.
How often should I apply grease to brake pads?
You should apply grease to brake pads every time you replace them. You may also need to apply grease if the brake pads are starting to make noise or if they are not moving freely.